Research project for climate-neutral shunting operation
As part of the sH2unter@ports research project, six project partners worked from December 2022 to Sepember 2024 on the question of how shunting locomotives can be operated in a climate-neutral manner in the port context and, in particular, investigated whether the implementation of a hydrogen-powered locomotive is possible. The project partners bremenports, Hamburg Port Authority, the rail transport company evb, the Institute for Energy and Circular Economy at Bremen University of Applied Sciences, the Smart Mobility Institute at Bremerhaven University of Applied Sciences and ALSTOM also looked at other alternative drives in order to evaluate which type of drive is the most efficient from a technical, economic and ecological perspective.
Introduction of the topic of climate-neutral shunting operations in seaports
The study’s areas of investigation were the seaport of Hamburg and the overseas port of Bremerhaven. Both seaports load over 50 % of seagoing cargo onto rail in hinterland transport, and the trend is rising.
The shunting companies take on the important task of distributing freight wagons to the terminals or to the various trains according to their destination for export and import. These run on electrified lines; the degree of electrification is around 44% in Hamburg and 64% in Bremerhaven. The rail infrastructure is usually not electrified, particularly on the so-called last mile routes, partly because this is often not technically possible at the transhipment facilities. The research project investigated the conversion of shunting operations to alternative drives, in particular hydrogen. The following aspects were analysed:
- Requirements for the infrastructure, safety aspects and logistical implementation
- Development of new zero-emission and reduced-emission shunting locomotives, as well as the conversion of existing locomotives
- Sustainability studies: incentive and assistance systems for energy-saving driving behaviour, economic and ecological studies
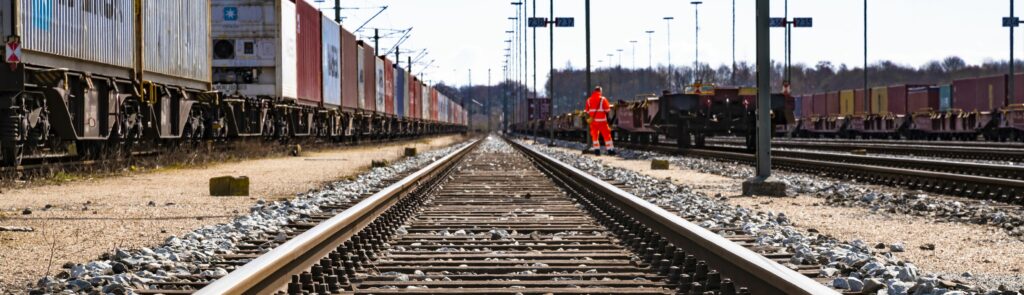
Adaptation of the infrastructure
In general, ports that have to implement the political target of climate neutrality will continue to be hubs for energy imports in the future, as numerous studies have shown (e.g. [1], p. 25 f) that the national energy demand will not be met by domestic energy production with renewable energies alone. Accordingly, it can be assumed that harbours will be expanded with H2 hubs for the landing of H2 in the future. This will make it possible to strategically plan for hydrogen. Network expansion and the further expansion of the harbour railway infrastructure with overhead lines are possible. The sH2unter@ports study compared possible drive systems. The premise here was that there should be no disruptions to operations during transshipment by the rail transport companies. Energy availability must also be guaranteed. In Bremerhaven, all shunting locomotives operated by the three rail transport companies are already fuelled with hydrogenated vegetable oil (HVO), which was included in the study.
Measurement series as a data basis
In the sh2unter@ports study, the performance requirements for shunting locomotives in the two harbour areas were examined in detail. A conventional G1000 diesel locomotive was equipped with measurement sensors to provide driving profiles for several weeks at high-resolution time intervals. The test locomotive was used in evb’s normal everyday operations. The following parameters were measured. The 15-week test runs in the seaports were completed at the end of September 2023, and the data was used to design different locomotive variants and check their performance in simulated shunting runs.
Overview of measurements on G1000
Torque on the wheel using strain gauges on the torque arm of the locomotive |
GPS data (speed, position, height) |
Acceleration |
Humidity |
Temperature |
Pulled force per strain gauge on the locomotive’s draw hook Inclination in the track |
Motor data such as torque, temperature and consumption |
Locomotive variants analysed
The following variants were analysed for the technical feasibility as well as for the ecological and economic studies:
V1: New-build locomotive with fuel cell & battery: It was shown that a locomotive with a fuel cell of approx. 220kW combined with a battery of at least 315kWh would fulfil the requirements in both seaports. On extreme days the consumption is up to 130kg, on average 80kg. It is therefore advisable to implement a hydrogen storage system of more than 130kg in order to meet the requirement of at least one day of operation without refuelling.
V2: New-build locomotive with overhead line & battery: For the overhead line variant, the existing overhead line systems were analysed and, assuming an automatic system for raising and lowering the pantograph, the performance of the battery in the non-overhead area was considered. For the days measured, it was found that a battery with a capacity of 420kWh should be sufficient. However, a stress test assuming insufficient charging times between uses revealed the limits of the system. A follow-up project should look at how additional overhead line islands can improve performance, and more driving profiles should also be considered.
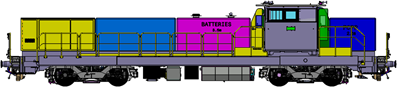
V3: Retrofit locomotive with H2-ICE as generator & battery system: Insofar as a conversion of the locomotive originally operated as a diesel-hydraulic to an electric drive system is feasible in terms of approval, a system consisting of a hydrogen combustion engine with direct injection (100% operated with hydrogen, Otto principle) with an output of 440 kW combined with a battery with 210 kWh capacity would be able to fulfil the driving profiles. The conversion studies of the existing locomotive show that up to 70kg of hydrogen can be stored on the locomotive. As this system requires up to 170kg of hydrogen on extreme days, an average of 110kg, it is clear that refuelling would be necessary at least twice a day, which would have to be reassessed from an operational perspective.
V4: Retrofit locomotive with H2-ICE via existing transmission: This technically simpler retrofit considers the conversion of the existing diesel engine to a hydrogen combustion engine with direct injection (100% fuelled with hydrogen, Otto principle). All systems apart from the diesel tank remain on the locomotive so that approx. 40kg of hydrogen can be stored. As this system requires up to 150kg of hydrogen on extreme days, 95kg on average, it is clear that refuelling would be necessary at least three times a day, which would have to be reassessed from an operational point of view.
Shunting operation with hydrogen is technically feasible, but operational measures must be considered due to the range. While conversions can be implemented more quickly and therefore represent a transitional option, a larger quantity of hydrogen can be stored in new vehicles by extending the vehicle (G1000 approx. 14m; new vehicles on the market sometimes 19m) and therefore the range requirements can be better realised. The variant with overhead line and battery fulfils the measured profile and can probably also be implemented for stress scenarios if the operational conditions are created, such as overhead line islands or charging devices at frequent stops as well as a technical device that ensures the automatic raising and lowering of the pantograph. A more in-depth examination of different locomotive types and applications is necessary for a fleet statement.
Incentive system for energy-saving driving behaviour
Incentive and assistance systems have the potential to have a positive impact on the energy and resource efficiency of a shunting locomotive. To quantify the specific potential for reducing fuel and the associated greenhouse gas emissions, several accompanying journeys were carried out with experienced locomotive drivers during the measurement period and various driving styles were simulated in shunting operations under real operating conditions. Thanks to the measurement electronics, it was possible to demonstrate the influence of the shunting crew’s driving behaviour on the locomotive’s fuel consumption. On this basis, incentive and assistance systems were investigated that can be implemented in the operation of a shunting locomotive and motivate shunting personnel to adopt a more sustainable driving style. Employees can be motivated to adopt more sustainable driving behaviour and coordinated logistics planning through suitable information-based, social and reward-based incentive systems.
The evaluation of the test drives revealed a concrete savings potential of 3.1 – 5.5 % in terms of fuel consumption through a change in driving behaviour. Assistance systems, such as a start-stop system, can reduce fuel consumption by up to 10.7 %. These potential savings have a similar effect on TTW greenhouse gas emissions and can already be realised today regardless of the drive technology used. In addition to savings in greenhouse gases and fuel, incentive and assistance systems also protect the wear parts on the locomotives and the infrastructure.
Economic analyses
Key Performance Indicators (KPI) were analysed which allow the operating and service quality of different locomotive variants and their development progress to be compared: including technical availability, range, maintenance costs and intervals and fuel availability.
In order to create the cost model developed according to the total cost of ownership approach, CAPEX and OPEX data were recorded using real operating data and the values from the test runs as the basis for variable and fixed cost accounting. The cost model includes a comparative evaluation of the diesel and HVO-powered shunting locomotives with the alternative locomotive variants. The variable cost calculation shows that fuel costs are currently (July 2024) a significant cost factor, particularly for locomotive variants powered by grey hydrogen. With a future decrease in demand for natural gas and an increase in imports as well as the domestic production of green hydrogen in Germany, a decrease in prices for both hydrogen variants can be expected. Cost drivers within the fixed cost calculation are primarily the expenses for major overhauls with component replacement, which mainly affect the variants with batteries. It should be noted that the prices for fuel cells and batteries are currently highly volatile on the market. In addition to analysing the current cost situation, the price development for future scenarios, the costs for necessary infrastructure measures and possible savings through the use of assistance systems were also taken into account.
Ecological analyses
The environmental impact of the shunting locomotives examined was analysed with the help of life cycle assessment studies. The basis for the comparison was, among other things, the use of different fuels (diesel, HVO, hydrogen and electricity from different sources, including wind, solar, German electricity mix), as well as the different drive technologies for hydrogen (fuel cell, hybrid, combustion engine). Operating parameters relevant for calculating the environmental impact were recorded and analysed during test drives in both Bremerhaven and Hamburg. In addition to the results of the test runs, further data on the locomotive itself and on the fuels used, operating resources, infrastructure, etc. were collected and included in the environmental assessment. The average service life of a shunting locomotive was taken into account as the assessment period. The evaluation itself was carried out with regard to various impact categories (e.g. climate protection, resource conservation). Other environmental impacts such as nitrogen oxide and particulate matter emissions in the vicinity of the port operations were also analysed. The aim was to identify the conditions under which shunting locomotives can be used in the most climate-friendly way possible.
Conclusion
The conversion of shunting operations to various drive options with hydrogen was classified as feasible. This applies to the necessary installation of infrastructure and refuelling systems, as well as to various types of locomotives powered by hydrogen. The driving data has shown that it is also possible to switch to hybrid drives with overhead lines and batteries over the last mile. Depending on the area of application, however, this would entail high costs for the infrastructure operators. The parties involved, the rail transport companies and, for example, locomotive leasing companies, require technology that can be used across the board. In future, when locomotives are deployed, the driving profile and other technical and infrastructural restrictions will have to be checked in order to be able to select the best technical, ecological and economic variant for operation. This study has analysed the tools required for this. This should reduce the effort required for such an investigation in the future – not only in the harbour context.